Exploring the Materials for Deadbreak Connectors and Their Impact on Performance
- sapowertech
- Jun 5, 2024
- 3 min read
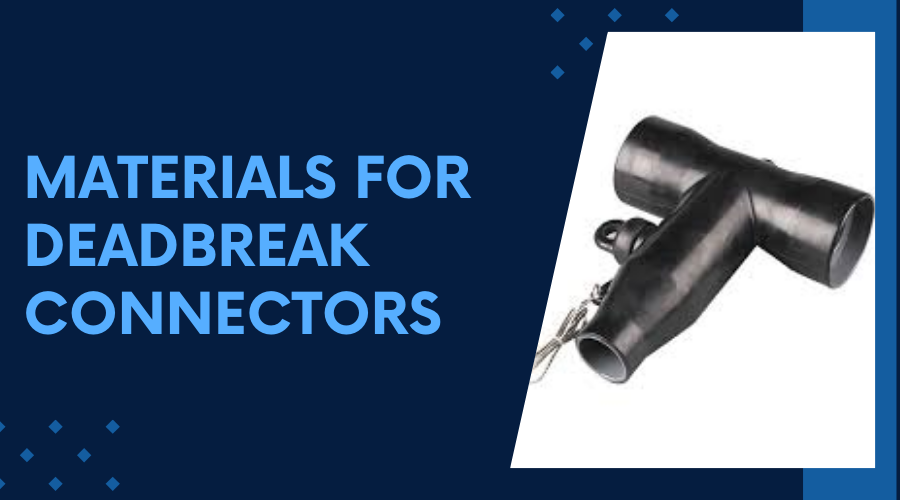
The choice of materials can significantly affect performance, durability, and reliability in electrical connections, especially in high-stress environments. Deadbreak connectors, widely used in medium—to high-voltage applications, are no exception. Deadbreak connector manufacturers choose different materials and examine their implications for performance, longevity, and overall effectiveness.
Copper: The Benchmark for Conductivity
Copper is often the go-to material for electrical connectors due to its excellent electrical and thermal conductivity. In deadbreak connectors, copper is typically used for the conductive path.
Advantages of Copper:
High Conductivity: Ensures efficient electrical flow with minimal resistance.
Thermal Management: Effective at dissipating heat generated by electrical currents.
Durability: Strong resistance to fatigue and wear.
Drawbacks of Copper:
Cost: Copper can be expensive, influencing the overall cost of the connectors.
Weight: Heavier than some alternative materials, which can be a factor in specific applications.
Aluminum: A Lightweight Alternative
Aluminum is another popular material choice, especially where weight and cost are significant considerations.
Advantages of Aluminum:
Lightweight: Easier to handle and install, particularly in large systems.
Cost-Effective: Generally cheaper than copper.
Corrosion Resistance: Forms a protective oxide layer that prevents further corrosion.
Drawbacks of Aluminum:
Lower Conductivity: Not as efficient as copper, requiring larger cross-sections to carry the same current.
Thermal Expansion: Expands more than copper when heated, which can affect long-term reliability.
Bimetallic Connectors: Combining Strengths
Bimetallic connectors combine the best properties of copper and aluminum, offering a balanced solution.
Advantages of Bimetallic Connectors:
Optimized Conductivity: Utilizes copper for high-conductivity areas and aluminum for structural parts.
Cost and Weight Balance: Achieves a compromise between the cost of copper and the lightweight nature of aluminum.
Corrosion Resistance: Effective in preventing galvanic corrosion when connecting aluminum cables to copper equipment.
Drawbacks of Bimetallic Connectors:
Complex Manufacturing: Requires precise engineering to bond different metals effectively.
Potential for Electrochemical Issues: Careful design is needed to prevent issues at the metal interface.
Stainless Steel: Durability in Harsh Environments
Stainless steel is used in components that require high strength and resistance to environmental factors.
Advantages of Stainless Steel:
Corrosion Resistance: Excellent in harsh, corrosive environments.
Mechanical Strength: High resistance to physical and mechanical stress.
Longevity: Durable and long-lasting, even in demanding conditions.
Drawbacks of Stainless Steel:
Conductivity: Much lower than copper and aluminum, usually not used for the primary conductive path.
Cost: More expensive than standard steel and some other materials.
Epoxy and Composite Materials: Insulation and Protection
Epoxy and composite materials are frequently used to insulate and protect components within deadbreak connectors.
Advantages of Epoxy and Composites:
High Insulation: Excellent dielectric properties, ensuring safety and reliability.
Durability: Resistant to environmental degradation, including UV exposure and moisture.
Lightweight: Contributes to easier handling and installation.
Drawbacks of Epoxy and Composites:
Thermal Limitations: Can degrade under high temperatures if not correctly designed.
Repairability: Damaged composite parts can be more challenging to repair than metal counterparts.
Rubber and Elastomers: Flexibility and Sealing
Rubber and elastomers are critical for sealing and ensuring flexibility in deadbreak connectors.
Advantages of Rubber and Elastomers:
Flexibility: Accommodates movement and thermal expansion.
Sealing Properties: Effective at preventing moisture and contaminants from entering the connection.
Durability: Resistant to wear and environmental factors.
Drawbacks of Rubber and Elastomers:
Aging: Can degrade over time due to exposure to ozone, UV, and other factors.
Temperature Sensitivity: Performance can vary significantly with temperature changes.
Choosing the Right Material for Specific Applications
The appropriate material for deadbreak connectors depends on the specific application and environmental conditions. Factors to consider include:
Electrical Requirements: Current-carrying capacity and thermal management needs.
Environmental Conditions: Exposure to moisture, chemicals, temperature extremes, and UV radiation.
Mechanical Stress: Physical forces and vibrations the connector will endure.
Cost Considerations: Budget constraints and cost-effectiveness.
Conclusion
In conclusion, the material choices for deadbreak connectors significantly impact their performance, durability, and reliability. Copper and aluminum remain primary choices for their conductive properties, while stainless steel, epoxy, and rubber materials provide the necessary strength, insulation, and flexibility. Bimetallic connectors offer a balanced solution, combining the strengths of different metals.
Understanding these materials and their characteristics allows for informed decisions that enhance the efficiency and longevity of electrical systems.
コメント